INNOVATIONS IN SCIENCE, TECHNOLOGY AND MATHEMATICS EDUCATION IN NIGERIA, Ebele C. Okigbo, Nneka R. Nnorom, Ernest O. Onwukwe [best reads .TXT] 📗
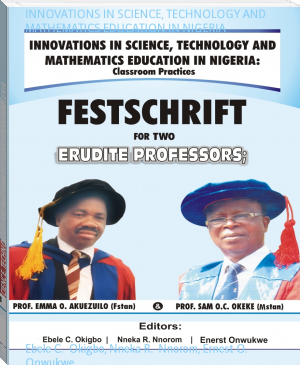
- Author: Ebele C. Okigbo, Nneka R. Nnorom, Ernest O. Onwukwe
Book online «INNOVATIONS IN SCIENCE, TECHNOLOGY AND MATHEMATICS EDUCATION IN NIGERIA, Ebele C. Okigbo, Nneka R. Nnorom, Ernest O. Onwukwe [best reads .TXT] 📗». Author Ebele C. Okigbo, Nneka R. Nnorom, Ernest O. Onwukwe
Add-on % = weight of treated foam- weight of untreated foam x 100
Weight of untreated foam 1
After glow time
The afterglow time was calculated using a stopwatch to find out the time in seconds between the times the flame extinguished and the time the materials stopped glowing (Abdulrahman, Mohammed, Garba, 2001; Garba and Eboatu, 1990).
Flame Propagation Rate (FP)
The sample was clamped vertically and then ignition at the base in a draught free room. The distance travelled as a stipulated time interval by the char front was measured and the rate of flame propagation was calculated as the vertical distance traversed per second (Garba and Eboatu, 1990).
Flame propagation rate= Distance travelled (cm)
Times (s)
Ignition time
The sample was clamped vertically at a distance of 5cm and ignited at the base. The ignition time was calculated by recording the time in seconds after the Bunsen burner, flame stroke the sample surface to the time when the sample caught fire (Garba and Eboatu, 1990)
Char Formation
The amount of char formed was obtained by first crushing the sample in a crucible and weighing the content. It was then put in an electrically heated muffle furnace tat 700Oc for 20 minutes and weighing the samples. It was calculated by dividing the weight of the material after burning by the weight of the material before burning multiplied by 100 (Ikeh, 2011).
Char % = Weight of material after burning x 100
Weight of material after burning 1
Results
The results of fire characteristics of polyurethane foam retarded with castor oil are presented in Table 2.
Table 2: Fire characteristics of polyurethane foam retarded with castor oil
Castor oil
Percentage
(%)
Weight in gram(g)
Add-on %
Ignition time in seconds (S)
Flame propagation rate
After glow time in seconds(S)
Char formation
C0 (blank)
C1
C2
C3
C4
_
5
10
15
20
145
185
190
230
270
_
27
31
58
86
3
8
12
16
20
9.3
5.2
2.6
1.8
1.4
55
22
18
10
6
26
The results obtained shows that the Add-on%, ignition time increases with increase in concentration of castor oil and the flame propagation rate, After-glow time and char formation decreases with increase in concentration of castor oil.
The result of the fire characteristics of polyurethane foam retarded with Ammoniumdihydrogen- phosphate are presented in table 4.
Table 3: The fire characteristics of polyurethane foam incorporated with Ammoniumdihydrogen – phosphate (ADP)
The result obtained shows no change in ignition time when 5% of Ammoniumdihydrogen-phosphate was added.
The Add-on%, ignition-time increases with increase in Ammoniumdihydrogen- phosphate and the flame propagation , the After- glow time , char- formation reduces in concentration of Ammo iumdihydrogen- phosphate.
Discussion
It is clear from Table 3 and 4 of the results that castor oil has a good flame retardant ability than Ammonium dihydrogen phosphate. The weight of the foam increases with increase in castor oil, more than that of Ammoniumdihydrogen phosphate. And the Add-on increases more in castor oil than Ammoniumdiydrogen phosphate due to the porosity index and density of the foam (Garba and Eboatu, 1990). The decrease in flame propagation shows that although the phosphorous compound in Ammoniumdihydrogen-phosphate acts by the formation of carbonaceous layer by the condensed phase and fragments that interrupt the radical chain mechanism. But cannot be compare to that of castor oil which increases foam density and rigidity thus increases the bond strength of the foam which offers a serious resistance to bond breaking thereby reducing flame propagation (Ikeh, 2011). The afterglow and char formation decreases in castor oil than Ammoniumdihydrogen- phosphate but the decrease is less than compared to that stated by khattab, et al, (1992). This may be due to concentrations of the flame retardant used. There is a decrease in the char -formation of the two flame retardants used which disagreed with the work of Onuegbu, Umoh, and Izuchukwu, (2012). This can be due to the type of flame retardant used and the concentration of the flame retardant. The ignition time increases higher in castor oil than Ammoniumdiydrogen phosphate with increase in concentration but much lower in the result of the study in accordance with Salisu and Said (2012) which has the higher ignition time for castor oil.
The result obtained from Table 3 and 4 shows the need to incorporate flame retardants in the production of polyurethane foam by manufactures. So as to retard flame in polyurethane foam, most especially the use of organic flame retardant like castor oil which are non- toxic, environmental friendly and essential flame retardant than inorganic flame retardant like Ammoniumdiydrogen phosphate.
Conclusion
From the result obtained shows that castor oil is better flame retardant than Ammoniumdiydrogen – phosphate (ADP) and retard flame more in polyurethane foams.
Castor oil flame retardants should be incorporated into polyurethane foam production because of its ability to retard flame efficiently in polyurethane foams than inorganic flame retardants like Ammoniumdiydrogen- phosphate. Castor oilsare cheaper, affordable and non- toxic to human and the environments.
References
Abdulrahman, F.W, Mohammed AU, Garba B. (2001) Effect of flame retardants treatment on thermal behavior of some fibrous materials. Nigeria Journal of Renewable Energy, 10 (2); 93-96.
Carignan C.C. Mcclean M.D (2013) “Predictors of tris (1, 3 dichloro – 2- propyl) Phosphate Metabolite in the urine of office workers” Environ int 55:56-61.
Garba, B, and Eboatu A, N (1990). Effect of flame retardant treatment on the thermal behavior of some tropical timbers. Journal of Applied/ Polymer Science,39 ,109- 112.
Herington, R, and Hock, K. (1991). Flexible polyurethane foam. Dow chemical company, Midland, M.I.P 201
Hollingbery LA; Hull TR (2012). “ The fire retardant effect of huntite in natural mixture with hydromagnestite polymer degradation and stability. 95 (12). 2213- 2225- doi. 10. 10161.
Hollingbery LA; Hull TR (2010). The thermal decomposition of huntite and hydromagnestite. Thermo chemical Acta . 509 (1-2): 1-11. Doi. 10.10161 j.tca 2010-06.012.
Hull, TR; Witkowski A; Hollingbery LA (2011) “Fire retardant action of mineral fillers”. Polymer degradation and stability 96 (8); 1462- 1469. Doi; 10.10161y. polymdegradstab. 2011-05.006.
Ikeh .O.P. (2011). Comparative analysis of flame characteristics of castor oil and some flame retardants in polyurethane foam systems. Nigeria Journal of Basic and Applied Science, 55-63
Khattab, M.A, Kandil S.H, Gad, A.M. Latif E.L and Morsis.E(1992). Effects of Condensed phase flame retardants on the ignition behavior of cotton fabrics. Fire malt, 16 (1); 1
Monoammonium phosphate (MAD) “ (PDF). WWW. Mosaicco. Com. Retrieved 2015-06-05
Onuegbu TU, Umoh ET, Iwuchukwu IE (2012) “Flame retardants effects on flexible polyurethane foam treated with Potassium Aluminum Sulphate”. Journal of Science and Technology.
Salisu, A.A and Said M.D, (2013) The use of castor oil as a flame retardant in polyurethane foam. ‘chem search’. Chemical Society of Nigeria, Kano Chapter, Nigeria.
Seymour , Raymond B; Kauffman , George B (1992). Polyurethane class of modern versatile materials. Journal of Chemical education, 69 (11), 909. Bib code: 1992Jched 69.9095 doi.10. 1021 / ed069p909.
Thomas, A (2005). Fats and Fatty oils. U11Mans Encyclopedia of industrial chemistry. Weinhemimi: Wiley – UCH. Doi: 10.1002/ 14356001.alo- 173.
Imprint
Publication Date: 07-01-2020
All Rights Reserved
Comments (0)