Shop Management, Frederick Winslow Taylor [most important books of all time .txt] 📗
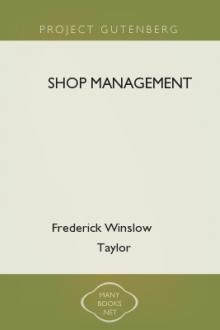
- Author: Frederick Winslow Taylor
- Performer: -
Book online «Shop Management, Frederick Winslow Taylor [most important books of all time .txt] 📗». Author Frederick Winslow Taylor
double or treble his output. They must see this pace maintained until
they are convinced that it is not a mere spurt; and, most important of
all, they must see the men who “get there” in this way receive a proper
increase in wages and become satisfied. It is only with these object
lessons in plain sight that the new theories can be made to stick. It
will be in presenting these object lessons and in smoothing away the
difficulties so that tile high speed can be maintained, and in assisting
to form public opinion in the shop, that the great efficiency of
functional foremanship under the direction of the planning room will
first become apparent.
In reaching the final high rate of speed which shall be steadily
maintained, the broad fact should be realized that the men must pass
through several distinct phases, rising from one plane of efficiency to
another until the final level is reached. First they must be taught to
work under an improved system of day work. Each man must learn how to
give up his own particular way of doing things, adapt his methods to the
many new standards, and grow accustomed to receiving and obeying
directions covering details, large and small, which in the past have
been left to his individual judgment. At first the workmen can see
nothing in all of this but red tape and impertinent interference, and
time must be allowed them to recover from their irritation, not only at
this, but at every stage in their upward march. If they have been
classed together and paid uniform wages for each class, the better men
should be singled out and given higher wages so that they shall
distinctly recognize the fact that each man is to be paid according to
his individual worth. After becoming accustomed to direction in minor
matters, they must gradually learn to obey instructions as to the pace
at which they are to work, and grasp the idea, first, that the planning
department knows accurately how long each operation should take; and
second, that sooner or later they will have to work at the required
speed if they expect to prosper. After they are used to following the
speed instructions given them, then one at a time they can be raised to
the level of maintaining a rapid pace throughout the day. And it is not
until this final step has been taken that the full measure of the value
of the new system will be felt by the men through daily receiving larger
wages, and by the company through a materially larger output and lower
cost of production. It is evident, of course, that all of the workmen in
the shop will not rise together from one level to another. Those engaged
in certain lines of work will have reached their final high speed while
others have barely taken the first step. The efforts of the new
management should not be spread out thin over the whole shop. They
should rather be focused upon a few points, leaving the ninety and nine
under the care of their former shepherds. After the efficiency of the
men who are receiving special assistance and training has been raised to
the desired level, the means for holding them there should be perfected,
and they should never be allowed to lapse into their old ways. This
will, of course, be accomplished in the most permanent way and rendered
almost automatic, either through introducing task work with a bonus or
the differential rate.
Before taking any steps toward changing methods the manager should
realize that at no time during the introduction of the system should any
broad, sweeping changes be made which seriously affect a large number of
the workmen. It would be preposterous, for instance, in going from day
to piece work to start a large number of men on piece work at the same
time. Throughout the early stages of organization each change made
should affect one workman only, and after the single man affected has
become used to the new order of things, then change one man after
another from the old system to the new, slowly at first, and rapidly as
public opinion in the shop swings around under the influence of proper
object lessons. Throughout a considerable part of the time, then, there
will be two distinct systems of management in operation in the same
shop; and in many cases it is desirable to have the men working under
the new system managed by an entirely different set of foremen, etc.,
from those under the old.
The first step, after deciding upon the type of organization, should be
the selection of a competent man to take charge of the introduction of
the new system. The manager should think himself fortunate if he can get
such a man at almost any price, since the task is a difficult and
thankless one and but few men can be found who possess the necessary
information coupled with the knowledge of men, the nerve, and the tact
required for success in this work. The manager should keep himself free
as far as possible from all active part in the introduction of the new
system. While changes are going on it will require his entire energies
to see that there is no falling off in the efficiency of the old system
and that the quality and quantity of the output is kept up. The mistake
which is usually made when a change in system is decided upon is that
the manager and his principal assistants undertake to make all of the
improvements themselves during their spare time, with the common result
that weeks, months, and years go by without anything great being
accomplished. The respective duties of the manager and the man in charge
of improvement, and the limits of the authority of the latter should be
clearly defined and agreed upon, always bearing in mind that
responsibility should invariably be accompanied by its corresponding
measure of authority.
The worst mistake that can be made is to refer to any part of the system
as being “on trial.” Once a given step is decided upon, all parties must
be made to understand that it will go whether any one around the place
likes it or not. In making changes in system the things that are given a
“fair trial” fail, while the things that “must go,” go all right.
To decide where to begin is a perplexing and bewildering problem which
faces the reorganizer in management when he arrives in a large
establishment. In making this decision, as in taking each subsequent
step, the most important consideration, which should always be first in
the mind of the reformer, is “what effect will this step have upon the
workmen?” Through some means (it would almost appear some especial
sense) the workman seems to scent the approach of a reformer even before
his arrival in town. Their suspicions are thoroughly aroused, and they
are on the alert for sweeping changes which are to be against their
interests and which they are prepared to oppose from the start. Through
generations of bitter experiences working men as a class have teamed to
look upon all change as antagonistic to their best interests. They do
not ask the object of the change, but oppose it simply as change. The
first changes, therefore, should be such as to allay the suspicions of
the men and convince them by actual contact that the reforms are after
all rather harmless and are only such as will ultimately be of benefit
to all concerned. Such improvements then as directly affect the workmen
least should be started first. At the same time it must be remembered
that the whole operation is of necessity so slow that the new system
should be started at as many points as possible, and constantly pushed
as hard as possible. In the metal working plant which we are using for
purposes of illustration a start can be made at once along all of the
following lines:
First. The introduction of standards throughout the works and office.
Second. The scientific study of unit times on several different kinds of
work.
Third. A complete analysis of the pulling, feeding power and the proper
speeding of the various machine tools throughout the place with a view
of making a slide rule for properly running each machine.
Fourth. The work of establishing the system of time cards by means of
which ultimately all of the desired information will be conveyed from
the men to the planning room.
Fifth. Overhauling the stores issuing and receiving system so as to
establish a complete running balance of materials.
Sixth. Ruling and printing the various blanks that will be required for
shop returns and reports, time cards, instruction cards, expense sheets,
cost sheets, pay sheet, and balance records; storeroom; tickler; and
maintenance of standards, system, and plant, etc.; and starting such
functions of the planning room as do not directly affect the men.
If the works is a large one, the man in charge of introducing the system
should appoint a special assistant in charge of each of the above
functions just as an engineer designing a new plant would start a number
of draftsmen to work upon the various elements of construction. Several
of these assistants will be brought into close contact with the men, who
will in this way gradually get used to seeing changes going on and their
suspicion, both of the new men and the methods, will have been allayed
to such an extent before any changes which seriously affect them are
made, that little or no determined opposition on their part need be
anticipated. The most important and difficult task of the organizer will
be that of selecting and training the various functional foremen who are
to lead and instruct the workmen, and his success will be measured
principally by his ability to mold and reach these men. They cannot be
found, they must be made. They must be instructed in their new functions
largely, in the beginning at least, by the organizer himself; and this
instruction, to be effective, should be mainly in actually doing the
work. Explanation and theory Will go a little way, but actual doing is
needed to carry conviction. To illustrate: For nearly two and one-half
years in the large shop of the Bethlehem Steel Company, one speed boss
after another was instructed in the art of cutting metals fast on a
large motor-driven lathe which was especially fitted to run at any
desired speed within a very wide range. The work done in this machine
was entirely connected, either with the study of cutting tools or the
instruction of speed bosses. It was most interesting to see these men,
principally either former gang bosses or the best workmen, gradually
change from their attitude of determined and positive opposition to that
in most cases of enthusiasm for, and earnest support of, the new
methods. It was actually running the lathe themselves according to the
new method and under the most positive and definite orders that produced
the effect. The writer himself ran the lathe and instructed the first
few bosses. It required from three weeks to two months for each man.
Perhaps the most important part of the gang boss’s and foreman’s
education lies ill teaching them to promptly obey orders and
instructions received not only from the superintendent or some official
high in the company, but from any member of the planning room whose
especial function it is to direct the rest of the works in his
particular line; and it may be accepted as an unquestioned fact that no
gang boss is fit to direct his men until after he has learned to
promptly obey instructions received from any proper source, whether he
likes his instructions and the
Comments (0)