Shop Management, Frederick Winslow Taylor [most important books of all time .txt] 📗
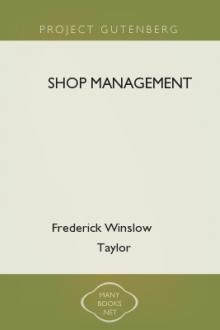
- Author: Frederick Winslow Taylor
- Performer: -
Book online «Shop Management, Frederick Winslow Taylor [most important books of all time .txt] 📗». Author Frederick Winslow Taylor
Proper time … . . 65 minutes
Bonus given first time job is done. 108 minutes
It is of the greatest importance that the man who has charge of
assigning tasks should be perfectly straightforward in all of his
dealings with the men. Neither in this nor in any other branch of the
management should a man make any pretense of having more knowledge than
he really possesses. He should impress the workmen with the fact that he
is dead in earnest, and that he fully intends to know all about it some
day; but he should make no claim to omniscience, and should always be
ready to acknowledge and correct an error if he makes one. This
combination of determination and frankness establishes a sound and
healthy relation between the management and men.
There is no class of work which cannot be profitably submitted to time
study, by dividing it into its time elements, except such operations as
take place in the head of the worker; and the writer has even seen a
time study made of the speed of an average and first-class boy in
solving problems in mathematics.
Clerk work can well be submitted to time study, and a daily task
assigned in work of this class which at first appears to be very
miscellaneous in its character.
One of the needs of modern management is that of literature on the
subject of time study. The writer quotes as follows from his paper on “A
Piece Rate System,” written in 1895:
“Practically the greatest need felt in an establishment wishing to start
a rate-fixing department is the lack of data as to the proper rate of
speed at which work should be done. There are hundreds of operations
which are common to most large establishments, yet each concern studies
the speed problem for itself, and days of labor are wasted in what
should be settled once for all, and recorded in a form which is
available to all manufacturers.
“What is needed is a handbook on the speed with which work can be done,
similar to the elementary engineering handbooks. And the writer ventures
to predict that such a book will before long be forthcoming. Such a book
should describe the best method of making, recording, tabulating, and
indexing time observations, since much time and effort are wasted by the
adoption of inferior methods.”
Unfortunately this prediction has not yet been realized. The writer’s
chief object in inducing Mr. Thompson to undertake a scientific time
study of the various building trades and to join him in a publication of
this work was to demonstrate on a large scale not only the desirability
of accurate time study, but the efficiency and superiority of the method
of studying elementary units as outlined above. He trusts that his
object may be realized and that the publication of this book may be
followed by similar works on other trades and more particularly on the
details of machine shop practice, in which he is especially interested.
As a machine shop has been chosen to illustrate the application of such
details of scientific management as time study, the planning department,
functional foremanship, instruction cards, etc., the description would
be far from complete without at least a brief reference to the methods
employed in solving the time problem for machine tools.
The study of this subject involved the solution of four important
problems:
First. The power required to cut different kinds of metals with tools of
various shapes when using different depths of cut and coarseness of
feed, and also the power required to feed the tool under varying
conditions.
Second. An investigation of the laws governing the cutting of metals
with tools, chiefly with the object of determining the effect upon the
best cutting speed of each of the following variables:
(a) The quality of tool steel and treatment of tools (i.e., in heating,
forging, and tempering them).
(b) The shape of tool (i.e., the curve or line of the cutting edge, the
lip angle, and clearance angle)
(c) The duration of cut or the length of time the tool is required to
last before being re-ground.
(d) The quality or hardness of the metal being cut (as to its effect on
cutting speed).
(e) The depth of the cut.
(f) The thickness of the feed or shaving
(g) The effect on cutting speed of using water or other cooling medium
on the tool.
Third. The best methods of analyzing the driving and feeding power of
machine tools and, after considering their limitations as to speeds and
feeds, of deciding upon the proper counter-shaft or other general
driving speeds.
Fourth. After the study of the first, second, and third problems had
resulted in the discovery of certain clearly defined laws, which were
expressed by mathematical formulae, the last and most difficult task of
all lay in finding a means for solving the entire problem which should
be so practical and simple as to enable an ordinary mechanic to answer
quickly and accurately for each machine in the shop the question, “What
driving speed, feed, and depth of cut will in each particular case do
the work in the quickest time?”
In 1881, in the machine shop of the Midvale Steel Company, the writer
began a systematic study of the laws involved in the first and second
problems above referred to by devoting the entire time of a large
vertical boring mill to this work, with special arrangements for varying
the drive so as to obtain any desired speed. The needed uniformity of
the metal was obtained by using large locomotive tires of known chemical
composition, physical properties and hardness, weighing from 1,500 to
2,000 pounds.
For the greater part of the succeeding 22 years these experiments were
carried on, first at Midvale and later in several other shops, under the
general direction of the writer, by his friends and assistants, six
machines having been at various times especially fitted up for this
purpose.
The exact determination of these laws and their reduction to formulae
have proved a slow but most interesting problem; but by far the most
difficult undertaking has been the development of the methods and
finally the appliances (i.e., slide rules) for making practical use of
these laws after they were discovered.
In 1884 the writer succeeded in making a slow solution of this problem
with the help of his friend, Mr. Geo. M. Sinclair, by indicating the
values of these variables through curves and laying down one set of
curves over another. Later my friend, Mr. H. L. Gantt, after devoting
about 1 1/2 years exclusively to this work, obtained a much more rapid
and simple solution. It was not, however, until 1900, in the works of
the Bethlehem Steel Company, that Mr. Carl G. Barth, with the assistance
of Mr. Gantt and a small amount of help from the writer, succeeded in
developing a slide rule by means of which the entire problem can be
accurately and quickly solved by any mechanic.
The difficulty from a mathematical standpoint of obtaining a rapid and
accurate solution of this problem will be appreciated when it is
remembered that twelve independent variables enter into each problem,
and that a change in any of these will affect the answer. The
instruction card can be put to wide and varied use. It is to the art of
management what the drawing is to engineering, and, like the latter,
should vary in size and form according to the amount and variety of the
information which it is to convey. In some cases it should consist of a
pencil memorandum on a small piece of paper which will be sent directly
to the man requiring the instructions, while in others it will be in the
form of several pages of typewritten matter, properly varnished and
mounted, and issued under the check or other record system, so that it
can be used time after time. A description of an instruction card of
this kind may be useful.
After the writer had become convinced of the economy of standard methods
and appliances, and the desirability of relieving the men as far as
possible from the necessity of doing the planning, while master mechanic
at Midvale, he tried to get his assistant to write a complete
instruction card for overhauling and cleaning the boilers at regular
periods, to be sure that the inspection was complete, and that while the
work was thoroughly done, the boilers should be out of use as short a
time as possible, and also to have the various elements of this work
done on piece work instead of by the day. His assistant, not having
undertaken work of this kind before, failed at it, and the writer was
forced to do it himself. He did all of the work of chipping, cleaning,
and overhauling a set of boilers and at the same time made a careful
time study of each of the elements of the work. This time study showed
that a great part of the time was lost owing to the constrained position
of the workman. Thick pads were made to fasten to the elbows, knees, and
hips; special tools and appliances were made for the various details of
the work; a complete list of the tools and implements was entered on the
instruction card, each tool being stamped with its own number for
identification, and all were issued from the tool room in a tool box so
as to keep them together and save time. A separate piece work price was
fixed for each of the elements of the job and a thorough inspection of
each part of the work secured as it was completed.
The instruction card for this work filled several typewritten pages, and
described in detail the order in which the operations should be done and
the exact details of each man’s work, with the number of each tool
required, piece work prices, etc.
The whole scheme was much laughed at when it first went into use, but
the trouble taken was fully justified, for the work was better done than
ever before, and it cost only eleven dollars to completely overhaul a
set of 300 H.P. boilers by this method, while the average cost of doing
the same work on day work without an instruction card was sixty-two
dollars.
Regarding the personal relations which should be maintained between
employers and their men, the writer quotes the following paragraphs from
a paper written in 1895. Additional experience has only served to
confirm and strengthen these views; and although the greater part of
this time, in his work of shop organization, has been devoted to the
difficult and delicate task of inducing workmen to change their ways of
doing things he has never been opposed by a strike.
“There has never been a strike by men working under this system,
although it has been applied at the Midvale Steel Works for the past
ten years; and the steel business has proved during this period the
most fruitful field for labor organizations and strikes. And this
notwithstanding the fact that the Midvale Company has never prevented
its men from joining any labor organization. All of the best men in the
company saw clearly that the success of a labor organization meant the
lowering of their wages in order that the inferior men might earn more,
and, of course, could not be persuaded to join.
“I attribute a great part of this success in avoiding strikes to the
high wages which the best men were able to earn with the differential
rates, and to the pleasant feeling fostered by this system; but this is
by no means the whole cause. It has for years been the policy
Comments (0)