Jute Fabric Defects, Sujai Das, Surajit Sengupta [best books to read in life .TXT] 📗
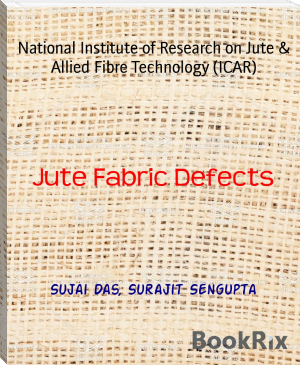
- Author: Sujai Das, Surajit Sengupta
Book online «Jute Fabric Defects, Sujai Das, Surajit Sengupta [best books to read in life .TXT] 📗». Author Sujai Das, Surajit Sengupta
Quality measurement is an important aspect during the production of textile fabrics in lowering costs and improving the finished product. Much of the fabric inspection is performed manually by human inspectors. Many defects are missed, and the inspection is inconsistent, the output depending on the training and the skill level of the human inspectors and also the mental and physical conditions of the inspector. Hence the textile industry has been moving towards automated fabric inspection system. An automated fabric inspection system can provide consistent results that correlate with the quality control standards of the textile industry. Fabric defect detection has been a long – felt need in the textile and apparel industry. Surveys carried out in the early 1975 shows that inadequate or inaccurate inspection of fabrics has led to fabric defects being missed out, which in turn had great effects on the quality and subsequent costs of the fabric finishing and garment manufacturing processes.
The weaving machine is one of the easiest and fastest ways of producing cloth and textile pieces. The automated defect detection and identification system enhance the product quality and result in improved quality to meet both the customer demand and to reduce the cost associated with off-quality. This process also reduces the manual work load associated with the inspection process. Off-line monitoring system has its own disadvantages when it is compared with that of on-line monitoring system. In the off-line monitoring system the produced fabric is taken to the inspection frame where the quality of the fabric is analyzed and the fabric is transfer to the successive process. But in the on-line monitoring system the inspection of the fabric is done simultaneously while the fabric is being produced. This paper describes about fault detection, positioning and classification of the faults occur in the weaving machine during weaving by using the principle of image processing, an automatic fabric evaluation system, which enable computerized defect detection – analysis of weaved fabrics. This method involves the process of analyzing the fabric image capture by a digital camera. The advantage for the manufacturer here is to get a warning when a certain amount of defect or imperfection occurs during the production of the fabric so that precautionary measures can be taken before the product hits the market. Wastage reduction through accurate and early stage detection of defects in fabrics is an important aspect of quality improvement. The problem of web inspection, articularly, is very important and complex and the research in this field is widely open.
Fabric texture refers to the feel of the fabric. It is smooth, rough, soft, velvety, silky, lustrous, and so on. The different textures of the fabric depend upon the types of weaves used. Textures are given to all types of fabrics, cotton, silk, wool, leather etc., There are more than 50 categories of fabric defects in the textile industry. Many of these defects have preferred orientation; either in the direction of motion (warp direction) or perpendicular to it (pick direction). Many defects are caused by machine malfunctions; others are due to faulty yarns. In textile, different types of defects are available i.e. hole, scratch, stretch, fly yarn, dirty spot, slub, cracked point,color bleeding etc; if not detected properly these faults can affect the production process massively. The objective of the proposed work is to identify whether the fabric is defective or not. If it is defective then identify the location and the type of the defect.
Defects in WeavingThe various types of defects of weaving are given below.
Broken Ends- If a warp is absent in the fabric for a very short or long distance and then this fabric defect is called broken ends..
Broken Picks- If a warp is absent in the fabric for a very short or long width and then this fabric defect is called broken picks.
Float-A float is a kind of defect where a warp or weft yarn floats over the fabric surface for a few container lengths due to missing of interlacement of two series of yarns..
Slugs-When the weft yarn is unclean and contains slugs and its diameter is irregular,
Holes-If there is any small holes present in the fabric and then it is a major fabric defect.The occurrence of hole, cut or tear which is self explanatory.
Oil Spot-Oil Spot on the fabric are caused by too much oiling on loom parts from other sources. Oil stains in most fabrics may be removed by scouring process.
Irregular Pick Density-If the pick density that is pick per inch varies due to mechanical fault then thick or thin place may be formed in the fabric.
Image AcquisitionThe first stage of any vision system is the image acquisition stage. Different types of camera can be used for this application such as CCD (Charged Coupled Device) camera, CMOS (Complementary Metal Oxide Semiconductor) camera, Digital camera, etc. The pixel value of these cameras is around 320 × 420 pixels. After the image has been obtained, various methods of processing can be applied to the image to perform different tasks. If the image has not been acquired satisfactorily then the intended tasks may not be achievable. The following are the various methods for image acquisition.
Laser Ranging Systems
Structured Light MethodsMoire
Fringe Methods
Shape from Shading Methods
Active and Passive Stereoscopic Methods
Gray Scale Image
The acquired image must be converted into gray scale to eliminate the hue and saturation information while retaining the luminance.
Filtering & Histogram Processing
A filter is defined by a kernel, which is a small array applied to each pixel and its neighbors within an image. In most applications, the center of the kernel is aligned with the current pixel, and is a square with an odd number of elements in each dimension. The process used to apply filters to an image is known as convolution, and may be applied in either the spatial or frequency domain. The CONVOL function performs this convolution process for an entire image.
Segmentation and Noise Removal
Segmentation involves partitioning an image into groups of pixels which are homogeneous with respect to some criterion. Different groups must not intersect each other and adjacent groups must be heterogeneous. The groups are called segments. Most digital images exist on a rectangular grid. This is primarily due to the arrangement of image sensors on camera and scanning equipment.
Digital images consist of many types of noise. Noise is the result of errors in the image acquisition process. There are several ways that noise can be introduced into an image, depending on how the image is created. If the image is scanned from a photograph made on film, the film grain is a source of noise. Noise can also be the result of damage to the film, or be introduced by the scanner itself. If the image is acquired directly in a digital format, the mechanism for gathering the data (such as a CCD detector) can introduce noise. Electronic transmission of image data can introduce noise.
Feature ExtractionFeature Extraction is a method of capturing visual content of images for indexing & retrieval.
• feature construction
• feature subset generation
• evaluation criterion definition
• evaluation criterion estimation
Textures can be rough or smooth, vertical or horizontal etc generally they capture patterns in the image data. Example repetitiveness and granularity.
• Texture features are
– Statistical measures
• Entropy
• Homogeneity
• Contrast
– Wavelets
– Fractals
Artificial Neural NetworkArtificial Neural networks have been developed as generalization of mathematicalmodels of human
Comments (0)